- Mantenimiento
- Mantenimiento Preventivo
- Mantenimiento Predictivo
- Mantenimiento Productivo Total (T.P.M.)
- Gerencia de Infraestructura y Mantenimiento
- Conclusiones
- Bibliografía
INTRODUCCIÓN
El mantenimiento no es una función "miscelánea", produce un bien real, que puede resumirse en: capacidad de producir con calidad, seguridad y rentabilidad.
Para nadie es un secreto la exigencia que plantea una economía globalizada, mercados altamente competitivos y un entorno variable donde la velocidad de cambio sobrepasa en mucho nuestra capacidad de respuesta. En este panorama estamos inmersos y vale la pena considerar algunas posibilidades que siempre han estado pero ahora cobran mayor relevancia.
Particularmente, la imperativa necesidad de redimensionar la empresa implica para el mantenimiento, retos y oportunidades que merecen ser valorados.
Debido a que el ingreso siempre provino de la venta de un producto o servicio, esta visión primaria llevó la empresa a centrar sus esfuerzos de mejora, y con ello los recursos, en la función de producción. El mantenimiento fue "un problema" que surgió al querer producir continuamente, de ahí que fue visto como un mal necesario, una función subordinada a la producción cuya finalidad era reparar desperfectos en forma rápida y barata.
Sin embargo, sabemos que la curva de mejoras increméntales después de un largo período es difícilmente sensible, a esto se una la filosofía de calidad total, y todas las tendencias que trajo consigo que evidencian sino que requiere la integración del compromiso y esfuerzo de todas sus unidades. Esta realidad ha volcado la atención sobre un área relegada: el mantenimiento. Ahora bien, ¿cuál es la participación del mantenimiento en el éxito o fracaso de una empresa? Por estudios comprobados se sabe que incide en:
· Costos de producción.
· Calidad del producto servicio.
· Capacidad operacional (aspecto relevante dado el ligamen entre competitividad y por citar solo un ejemplo, el cumplimiento de plazos de entrega).
· Capacidad de respuesta de la empresa como un ente organizado e integrado: por ejemplo, al generar e implantar soluciones innovadoras y manejar oportuna y eficazmente situaciones de cambio.
· Seguridad e higiene industrial, y muy ligado a esto.
· Calidad de vida de los colaboradores de la empresa.
· Imagen y seguridad ambiental de la compañía.
Como se desprende de argumentos de tal peso, " El mantenimiento no es una función "miscelánea", produce un bien real, que puede resumirse en: capacidad de producir con calidad, seguridad y rentabilidad. Ahora bien, ¿dónde y cómo empezar a potenciar a nuestro favor estas oportunidades? Quizá aquí pueda encontrar algunas pautas.
MANTENIMIENTO
La labor del departamento de mantenimiento, está relacionada muy estrechamente en la prevención de accidentes y lesiones en el trabajador ya que tiene la responsabilidad de mantener en buenas condiciones, la maquinaria y herramienta, equipo de trabajo, lo cual permite un mejor desenvolvimiento y seguridad evitando en parte riesgos en el área laboral.
Características del Personal de Mantenimiento
El personal que labora en el departamento de mantenimiento, se ha formado una imagen, como una persona tosca, uniforme sucio, lleno de grasa, mal hablado, lo cual ha traído como consecuencia problemas en la comunicación entre las áreas operativas y este departamento y un más concepto de la imagen generando poca confianza.
Breve Historia de la Organización del Mantenimiento
La necesidad de organizar adecuadamente el servicio de mantenimiento con la introducción de programas de mantenimiento preventivo y el control del mantenimiento correctivo hace ya varias décadas en base, fundamentalmente, al objetivo de optimizar la disponibilidad de los equipos productores.
Posteriormente, la necesidad de minimizar los costos propios de mantenimiento acentúa esta necesidad de organización mediante la introducción de controles adecuados de costos.
Más recientemente, la exigencia a que la industria está sometida de optimizar todos sus aspectos, tanto de costos, como de calidad, como de cambio rápido de producto, conduce a la necesidad de analizar de forma sistemática las mejoras que pueden ser introducidas en la gestión, tanto técnica como económica del mantenimiento. Es la filosofía de la terotecnología. Todo ello ha llevado a la necesidad de manejar desde el mantenimiento una gran cantidad de información.
Objetivos del Mantenimiento
El diseño e implementación de cualquier sistema organizativo y su posterior informatización debe siempre tener presente que está al servicio de unos determinados objetivos. Cualquier sofisticación del sistema debe ser contemplada con gran prudencia en evitar, precisamente, de que se enmascaren dichos objetivos o se dificulte su consecución.
En el caso del mantenimiento su organización e información debe estar encaminada a la permanente consecución de los siguientes objetivos
· Optimización de la disponibilidad del equipo productivo.
· Disminución de los costos de mantenimiento.
· Optimización de los recursos humanos.
· Maximización de la vida de la máquina.
Criterios de la Gestión del Mantenimiento
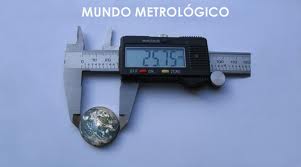
Mantenimiento
Es un servicio que agrupa una serie de actividades cuya ejecución permite alcanzar un mayor grado de confiabilidad en los equipos, máquinas, construcciones civiles, instalaciones.
Objetivos del Mantenimiento
· Evitar, reducir, y en su caso, reparar, las fallas sobre los bienes precitados.
· Disminuir la gravedad de las fallas que no se lleguen a evitar.
· Evitar detenciones inútiles o para de máquinas.
· Evitar accidentes.
· Evitar incidentes y aumentar la seguridad para las personas.
· Conservar los bienes productivos en condiciones seguras y preestablecidas de operación.
· Balancear el costo de mantenimiento con el correspondiente al lucro cesante.
· Alcanzar o prolongar la vida útil de los bienes.
El mantenimiento adecuado, tiende a prolongar la vida útil de los bienes, a obtener un rendimiento aceptable de los mismos durante más tiempo y a reducir el número de fallas.
Decimos que algo falla cuando deja de brindarnos el servicio que debía darnos o cuando aparecen efectos indeseables, según las especificaciones de diseño con las que fue construido o instalado el bien en cuestión.
Clasificación de las Fallas
Para ver el gráfico seleccione la opción "Descargar"
Fallas Tempranas
Ocurren al principio de la vida útil y constituyen un porcentaje pequeño del total de fallas. Pueden ser causadas por problemas de materiales, de diseño o de montaje.
Fallas adultas
Son las fallas que presentan mayor frecuencia durante la vida útil. Son derivadas de las condiciones de operación y se presentan más lentamente que las anteriores (suciedad en un filtro de aire, cambios de rodamientos de una máquina, etc.).
Fallas tardías
Representan una pequeña fracción de las fallas totales, aparecen en forma lenta y ocurren en la etapa final de la vida del bien (envejecimiento de la aislación de un pequeño motor eléctrico, perdida de flujo luminoso de una lampara, etc.
Tipos de Mantenimiento
Para ver el gráfico seleccione la opción "Descargar"
Mantenimiento para Usuario
En este tipo de mantenimiento se responsabiliza del primer nivel de mantenimiento a los propios operarios de máquinas.
Es trabajo del departamento de mantenimiento delimitar hasta donde se debe formar y orientar al personal, para que las intervenciones efectuadas por ellos sean eficaces.
Mantenimiento correctivo
Es aquel que se ocupa de la reparacion una vez se ha producido el fallo y el paro súbito de la máquina o instalación. Dentro de este tipo de mantenimiento podríamos contemplar dos tipos de enfoques:
Mantenimiento paliativo o de campo (de arreglo)
Este se encarga de la reposición del funcionamiento, aunque no quede eliminada la fuente que provoco la falla.
Mantenimiento curativo (de reparación)
Este se encarga de la reparación propiamente pero eliminando las causas que han producido la falla.
Suelen tener un almacén de recambio, sin control, de algunas cosas hay demasiado y de otras quizás de más influencia no hay piezas, por lo tanto es caro y con un alto riesgo de falla.
Mientras se prioriza la reparación sobre la gestión, no se puede prever, analizar, planificar, controlar, rebajar costos.
Conclusiones
La principal función de una gestión adecuada del mantenimiento consiste en rebajar el correctivo hasta el nivel óptimo de rentabilidad para la empresa.
El correctivo no se puede eliminar en su totalidad por lo tanto una gestión correcta extraerá conclusiones de cada parada e intentará realizar la reparacion de manera definitiva ya sea en el mismo momento o programado un paro, para que esa falla no se repita.
Es importante tener en cuenta en el análisis de la política de mantenimiento a implementar, que en algunas máquinas o instalaciones el correctivo será el sistema más rentable.
Historia
A finales del siglo XVIII y comienzo del siglo XIXI durante la revolución industrial, con las primeras máquinas se iniciaron los trabajos de reparacion, el inicio de los conceptos de competitividad de costos, planteo en las grandes empresas, las primeras preocupaciones hacia las fallas o paro que se producían en la producción. Hacia los años 20 ya aparecen las primeras estadisticas sobre tasas de falla en motores y equipos de aviacion.
Ventajas
· Si el equipo esta preparado la intervención en el fallo es rápida y la reposición en la mayoría de los casos será con el mínimo tiempo.
· No se necesita una infraestructura excesiva, un grupo de operarios competentes será suficiente, por lo tanto el costo de mano de obra será mínimo, será más prioritaria la experiencia y la pericia de los operarios, que la capacidad de análisis o de estudio del tipo de problema que se produzca.
· Es rentable en equipos que no intervienen de manera instantanea en la producción, donde la implantacion de otro sistema resultaría poco económico.
Desventajas
· Se producen paradas y daños imprevisibles en la produccion que afectan a la planifiacion de manera incontrolada.
· Se cuele producir una baja calidad en las reparaciones debido a la rapidez en la intervención, y a la prioridad de reponer antes que reparar definitivamente, por lo que produce un hábito a trabajar defectuosamente, sensación de insatisfacción e impotencia, ya que este tipo de intervenciones a menudo generan otras al cabo del tiempo por mala reparación por lo tanto será muy difícil romper con esta inercia.
Mantenimiento Preventivo
Este tipo de mantenimiento surge de la necesidad de rebajar el correctivo y todo lo que representa. Pretende reducir la reparación mediante una rutina de inspecciones periodicas y la renovación de los elementos dañados, si la segunda y tercera no se realizan, la tercera es inevitable.
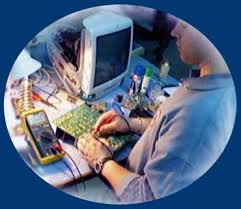
Historia:
Durante la segunda guerra mundial, el mantenimiento tiene un desarrollo importante debido a las aplicaciones militares, en esta evolución el mantenimiento preventivo consiste en la inspección de los aviones an tes de cada vuelo y en el cambio de algunos componentes en función del número de horas de funcionamiento.
Caracteristicas:
Basicamente consiste en programar revisiones de los equipos, apoyandose en el conocimiento de la máquina en base a la experiencia y los hist´ricos obtenidos de las mismas. Se confecciona un plan de mantenimiento para cada máquina, donde se realizaran las acciones necesarias, engrasan, cambian correas, desmontaje, limpieza, etc.
Ventajas:
· Se se hace correctamente, exige un conocimiento de las máquinas y un tratamiento de los históricos que ayudará en gran medida a controlar la maquinaria e instalaciones.
· El cuidado periódico conlleva un estudio óptimo de conservación con la que es indispensable una aplicación eficaz para contribuir a un correcto sistema de calidad y a la mejora de los contínuos.
· Reducción del correctivo representará una reducción de costos de producción y un aumento de la disponibilidad, esto posibilita una planificación de los trabajos del departamento de mantenimiento, así como una previsión de l.los recambios o medios necesarios.
· Se concreta de mutuo acuerdo el mejor momento para realizar el paro de las instalaciones con producción.
Desventajes:
· Representa una inversión inicial en infraestructura y mano de obra. El desarrollo de planes de mantenimiento se debe realizar por tecnicos especializados.
· Si no se hace un correcto análisis del nivel de mantenimiento preventiventivo, se puede sobrecargar el costo de mantenimiento sin mejoras sustanciales en la disponibilidad.
· Los trabajos rutinarios cuando se prolongan en el tiempo produce falta de motivación en el personal, por lo que se deberan crear sitemas imaginativos para convertir un trabajo repetitivo en un trabajo que genere satisfacción y compromiso, la implicación de los operarios de preventivo es indispensable para el éxito del plan.
Mantenimiento Predictivo
Este tipo de mantenimiento se basa en predecir la falla antes de que esta se produzca. Se trata de conseguir adelantarse a la falla o al momento en que el equipo o elemento deja de trabajar en sus condiciones óptimas. Para conseguir esto se utilizan herramientas y técnicas de monitores de parametros físicos.
Historia
Durante los años 60 se inician técnicas de verificación mecánica a través del análisis de vibraciones y ruidos si los primeros equipos analizadores de espectro de vibraciones mediante la FFT (Transformada rápida de Fouries), fuerón creados por Bruel Kjaer.
Ventajas
· La intervención en el equipo o cambio de un elemento.
· Nos obliga a dominar el proceso y a tener unos datos técnicos, que nos comprometerá con un método cientifico de trabajo riguroso y objetivo.
Desventajas
· La implantancion de un sistema de este tipo requiere una inversion inicial imoprtante, los equipos y los analizadores de vibraciones tienen un costo elevado. De la misma manera se debe destinar un personal a realizar la lectura periodica de datos.
· Se debe tener un personal que sea capaz de interpretar los datos que generan los equipos y tomar conclusiones en base a ellos, trabajo que requiere un conocimiento técnico elevado de la aplicación.
· Por todo ello la implantación de este sistema se justifica en máquina o instalaciones donde los paros intempestivos ocacionan grandes pérdidas, donde las paradas innecesarias ocacionen grandes costos.
Mantenimiento Productivo Total (T.P.M.)
Mantenimiento productivo total es la traducción de TPM (Total Productive Maintenance). El TPM es el sistema Japonés de mantenimiento industrial la letra M representa acciones de MANAGEMENT y Mantenimiento. Es un enfoque de realizar actividades de dirección y transformación de empresa. La letra P está vinculada a la palabra "Productivo" o "Productividad" de equipos pero hemos considerado que se puede asociar a un término con una visión más amplia como "Perfeccionamiento" la letra T de la palabra "Total" se interpresta como "Todas las actividades que realizan todas las personas que trabajan en la empresa"
Definición
Es un sistema de organización donde la responsabilidad no recae sólo en el departamento de mantenimiento sino en toda la estructura de la empresa "El buen funcionamiento de las máquinas o instalaciones depende y es responsabilidad de todos".
Objetivo
El sistema esta orientado a lograr:
· Cero accidentes
· Cero defectos.
· Cero fallas.
Historia
Este sistema nace en Japón, fue desarrollado por primera vez en 1969 en la empresa japonesa Nippondenso del grupo Toyota y de extiende por Japón durante los 70, se inicia su implementación fuera de Japón a partir de los 80.
Ventajas
· Al integrar a toda la organización en los trabajos de mantenimiento se consigue un resultado final más enriquecido y participativo.
· El concepto está unido con la idea de calidad total y mejora continua.
Desventajas
· Se requiere un cambio de cultura general, para que tenga éxito este cambio, no puede ser introducido por imposición, requiere el convencimiento por parte de todos los componentes de la organización de que es un beneficio para todos.
· La inversión en formación y cambios generales en la organización es costosa. El proceso de implementación requiere de varios años.
Conceptos Generales de Solución de Problemas
Para ver el gráfico seleccione la opción "Descargar"
Método Implementación Gestión Mantenimiento
Leer más: https://www.monografias.com/trabajos15/mantenimiento-industrial/mantenimiento-industrial.shtml#MANTEN#ixzz2jJa991cJ
Historia y Evolución del Mantenimiento
El concepto ha ido evolucionando desde la simple función de arreglar y reparar los equipos para asegurar la producción (ENTRETENIMIENTO) hasta la concepción actual del MANTENIMIENTO con funciones de prevenir, corregir y revisar los equipos a fin de optimizar el coste global.
La historia de mantenimiento acompaña el desarrollo Técnico-Industrial de la humanidad. Al final del siglo XIX, con la mecanización de las industrias, surgió la necesidad de las primeras reparaciones.
Desde la Revolución Industrial, podemos definir, a grandes rasgos, las siguientes etapas en la evolución del mantenimiento:
- Hasta 1945
• Reparación Averías.
• Mantenimiento Correctivo.
- 1945 a 1980
• Relación entre Probabilidad de Fallo y Edad.
• Mantenimiento Preventivo Programado.
• Sistema de Planificación.
- 1980 a 1990
• Mantenimiento Preventivo Condicional.
• Análisis Causa Efecto.
• Participación de Producción (TPM).
- 1990 +
• Proceso de Mantenimiento.
• Calidad Total.
• Mantenimiento Fuente de Beneficio.
• Compromiso de Todos los Departamentos.
• Mantenimiento Basado en el Riesgo (RBM).
Organización del Mantenimiento
Los dos aspectos organizativos que afectan a la estructuración del mantenimiento son:
a) Dependencia Jerárquica.
- Departamentos dependientes de la dirección y al mismo nivel que fabricación.
- Integrados en la producción para facilitar la comunicación, colaboración y combinación.
b) Centralización/Descentralización.
- Estructura piramidal, con dependencia de una sola cabeza para toda la organización.
- Existencia de diversos departamentos de mantenimiento establecidos por plantas productivas ó cualquier otro criterio geográfico
Del análisis de las ventajas e inconvenientes de cada tipo de organización se deduce que la organización ideal es la "Centralización Jerárquica junto a una descentralización geográfica".
La metrología se puede definir como la Ciencia que estudia los Sistemas de Unidades, Métodos y Normas de los Instrumentos de medición en general.
En este Curso aprenderemos los conceptos básicos de Metrología Industrial y sus aplicaciones tanto en el campo legal como en el científico e industrial.
La metrología dimensional tambien es conocida como metrología geométrica. La metrología geométrica dimensional tiene el siguiente campo de aplicación:
-Interiores
-Exteriores
-Profundidades
-Angulos cualesquiera
-Rugosidad
-Forma por elementos aislados
Rectitud
Planitud
Circularidad
Cilindridad
Forma de una línea
Forma de una superficie
-Orientacion por elementos aislados
Paralelismo
Perpendicularidad
Inclinación
-Posición por elementos asociados
Localización de un elemento
Concentricidad
Coaxiabilidad
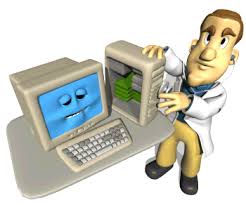
¿Alguien podrá conseguir un dibujo de ejemplo para cada aplicación?, podemos comenzar con las aplicaciones de longitud.
Publicado por Francisco Estrada García en 11:39 No hay comentarios: Enlaces a esta entrada
Es muy común hoy en día ver que los productos son elaborados en diferentes paises, inclusive paises de los que no es originaria la empresa. Gracias a esa familiaridad con los productos nos damos cuenta que el empaque del producto o el mísmo producto contiene símbolos inclusive texto que indica que para la elaboración de ese producto se han seguido las normas que aplican en esos paises o normas internacionales. Un símbolo muy común que es internacional es el que muestra la imagen de abajo, en esta imagen se puede observar un símbolo en cada una de las puertas, este simbolo significa que es un baño para damas y otro para caballeros.

Las normas pretenden dar solución a problemas generales, pero no sólo son simbolos los utilizados para seguir normas, tambien se puede incluir reglamentos y procedimientos (algunos de estos muy complejos).
El objetivo de las normas es obtener productos y servicios que cumplan con los requerimientos de los usuarios o clientes.
Existen las normas internacionales ISO, que son elaboradas por la International Organization for Standardization. Por ello el nombre de estas normas.
En México existen las normas oficiales mexicanas y las normas mexicanas, las primeras son de caracter obligatorio las segundas pueden servir como un apoyo a las empresas.
Las normas mexicanas y las oficiales mexicanas son elaboradas por los organismos nacionales de normalización, acontinuación se muestra un listado de estas:
- SOCIEDAD MEXICANA DE NORMALIZACIÓN Y CERTIFICACIÓN, S.C. (NORMEX)
- INSTITUTO MEXICANO DE NORMALIZACIÓN Y CERTIFICACIÓN, A. C. (IMNC)
- ASOCIACIÓN NACIONAL DE NORMALIZACIÓN Y CERTIFICACIÓN, A.C. (ANCE)
- INSTITUTO NACIONAL DE NORMALIZACIÓN TEXTIL, A.C. (INNTEX)
- ORGANISMO NACIONAL DE NORMALIZACIÓN Y CERTIFICACIÓN DE LA CONSTRUCCIÓN Y EDIFICACIÓN, S.C. (ONNCCE)
- NORMALIZACIÓN Y CERTIFICACIÓN ELECTRÓNICA, A.C. (NYCE)
Todas estas organizaciones son evaluadas por la direccion general de normas a travéz de la direccion de normalización.
La siguiente figura muestra un diagrama del esquema mexicano de normalización (haga clic sobre ella para maximizar la imagen).
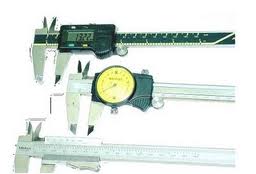

Figura1: Esquema mexicano de normalización
La figura anterior muestra en la parte principal a la Dirección General de Normas, debajo se encuentra la dirección general adjunta de operación. y al mismo nivel y por debajo de las dos anteriores se encuentran: Dirección de normalización, Dirección de normalización internacional, Dirección de metrología, Direcciónde evaluacion de la conformidad, Dirección de promoción, Dirección de gestión de la calidad y por último la subdirección de informática.
Publicado por Francisco Estrada García en 15:06 1 comentario: Enlaces a esta entrada
INTRODUCCION
La finalidad de la quinta unidad del curso de ingeniería eléctrica 1 es dar una visión general de los principales conceptos de metrología y normalización. Esto con la finalidad de establecer una base de conocimiento suficiente que permita a los estudiantes el manejo adecuado de los instrumentos y equipos de medición.
Etimológicamente, la palabra Metrología proviene de los vocablos griegos metros medida y logos tratado. La concepción de la metrología debe, en un principio, ser tan antigua como la humanidad misma y está unida a preguntas fundamentales como, tengo mucho, tengo poco, no tengo nada. De la misma manera las divisiones principales de la metrología corresponden a las nociones cerca-lejos, rápido-lento, liviano-pesado, claro-oscuro, duro-suave, frío-caliente, silencio-ruido. Todas estas expresiones reflejan la necesidad del ser humano de cuantificar todo aquello que lo rodea, primero de manera individual y después como sociedades, naciones y regiones del mundo, a través de comparaciones con unidades generalmente aceptadas.
Debido a lo anterior se puede definir a la Metrología como la Ciencia de las Mediciones, y que medir es comparar con algo (unidad) que se tomo como base de comparación.
OBJETIVOS
GENERAL
Determinar la importancia que tiene la metrología en la vida diría del ser humano, pues tiende a ser una actividad tan cotidiana, por ser la ciencia de las mediciones.
ESPECIFICOS
1- Conocer la clasificación de la metrología según el ámbito de aplicación. Como la aplicación de cada una de esta clasificación.
2- Conocer alguna de las áreas de la metrología como lo son la metrología eléctrica, metrología física, metrología de materiales, metrología mecánica y metrología de microbiología y laboratorios clínicos, entre otras que existen.
3- Conocer las maneras en que se presentan las incertidumbres propias de cada ensayo realizado en...
sistemas de trabajo "tiempos y movimientos"
es una actividad que va coordinada que tiene que ver con el trabajo "tiempos" actividad que implica la técnica de establecer un estándar de tiempo para realizar una tarea determinada, con base en la medición del contenido del trabajo del método prescrito, con la debida consideración de la fatiga y las demoras personales y los retrasos inevitables.
"movimientos" análisis cuidadoso de los diversos movimientos que efectúa el cuerpo al ejecutar un trabajo, se puede aplicar en dos formas el estudio visual de los movimientos y el estudio de los micromovimientos. El primero se aplica más frecuentemente por su mayor simplicidad y menor costo, el segundo sólo resulta factible cuando se analizan labores de mucha actividad cuya duración y repetición son elevadas.
diagrama bimanual
muestra todos los movimientos realizados por la mano izquierda y por la mano derecha, indicando la relación entre ellas, el diagrama bimanual sirve principalmente para estudiar operaciones repetitivas y en ese caso se registra un solo ciclo completo de trabajo. Para representar las actividades se emplean los mismos símbolos que se utilizan en los diagramas de proceso pero se les atribuye un sentido ligeramente distinto para que abarquen más detalles
para elaborar estos diagramas ese necesario tomar en cuenta:
- Estudiar el ciclo de las operaciones varias veces antes de comenzar las anotaciones.
- Registrar una sola mano cada vez.
- Registrar unos pocos símbolos cada vez.
consideraciones para aplicar un nuevo método de trabajo
la primera cuestión que debe resolverse es con que criterio debe seleccionarse el trabajo a estudiar
puede hacerse desde el "punto de vista humano" los primeros cuyo método deba mejorarse son los de mayor riesgo de accidentes y los más peligrosos en los que se manipulen sustancias toxicas.
Desde el "punto de vista económico". se debe dar preferencia a los trabajos cuyo valor represente un alto porcentaje sobre el costo del producto terminado, ya que las mejoras que se introduzcan, por pequeñas que sean, serán más interesantes económicamente que
grandes mejoras aplicadas.
Una vez registrados todos los detalles de que consta el trabajo, el siguiente paso es analizarlos para ver que acciones se pueden tomar para desarrollar un nuevo método para ejecutar el trabajo, "es necesario considerar las respuestas obtenidas"
Antes de aplicar el nuevo método es necesario tener la seguridad de que la
solución es practica bajo las condiciones de trabajo en que se va a operar.
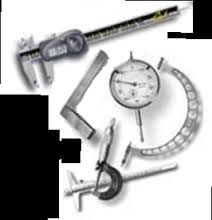